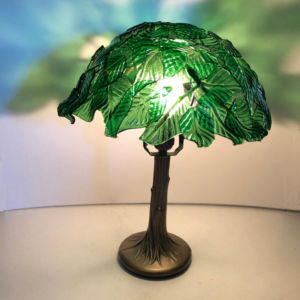
Ever wonder how to make a realistic fused leaf element for your masterpiece? Frit castings are ok but they are thick and hard to incorporate in your fused landscape. We have found the solution to this quandary. We are introducing the new NatureScape MOLDS that are two sided, realistic, leaf molds that produce slumped glass…